Leila Ben-Gacem follows an iconic hat whose production journey travels across Tunisia.
(A message to the reader in English.)
(A message to the reader in Arabic.)
At souk el Chaouachia in Tunis Medina, you pass by chaouachi (chechia artisan) little workshops. You find them busy in their working overalls, brushing, ironing, checking the finishing or counting chechias. At first, it looks like their world goes around their 3 by 5m store with boxes of chechia piled ground to roof. You ask a chaouachi a simple question “How is the chechia made?” and they give you a gentle smile, a smile that you would get from a rocket scientist when you ask “How does the rocket leave the earth?”. It might seem to be an arrogant smile, but, hey, if you dig deeper into the subject, you realise the entrepreneurial might of the simple chaouachi.
To help you grasp our national global brand, allow me to be a chaouachi, and share with you what I go through in my business to get the little chechia in a beautiful box at my chaouachia souk store. First I need to import wool. I know what you are thinking, why import wool? Don’t we have sheep? Yes, we do, but their fur is too curly and the finished chechia will not be soft enough. To import an important quantity, chechia artisans make a group order. One or two months later, a container arrives full of wool yarn. The wool exporter, gets his money in full, since goods were delivered, but we are still far from having a finished chechia.
The wool is then distributed to women, who crochet the kabbouss (the base of the chechia) from home in several rural Bizerte towns or Ariana. Each artisan crochets about half a dozen a day maximum. Once the women artisans have crouched all the wool yarn they received, I receive it into my shop in the medina, check the quality of each kabbouss, and pay the ladies each depending on her quality and quantity.
Now my kabbouss goes to women artisans in the Medina, who stitch my own logo onto each kabbouss. This simple stitch logo is unique for each chaouachi. The kabbouss then travels to Battan, where the felting and dying process takes place at a felting factory that was constructed near Majreda River about 100 years ago. At Battan, my kabbouss gets all wet and beaten up until it shrinks from a huge crocheted white bag into a little white sad chechia.
From Battan, the beaten-up chechia comes back to my store for inspection, and I know which ones out of Battan are mine because the little stitched logo shrunk in size but survives the beating. Once I inspect my chechias, I send them to Al Alya, where many families brush them with a plant called kardesh that Anadalousians used to use for their hats. When they immigrated to North Africa, the chechia brushing artisans settled in AL Alya, where they were able to plant the kardesh plants they brought with them to continue their craft wherever they settle.
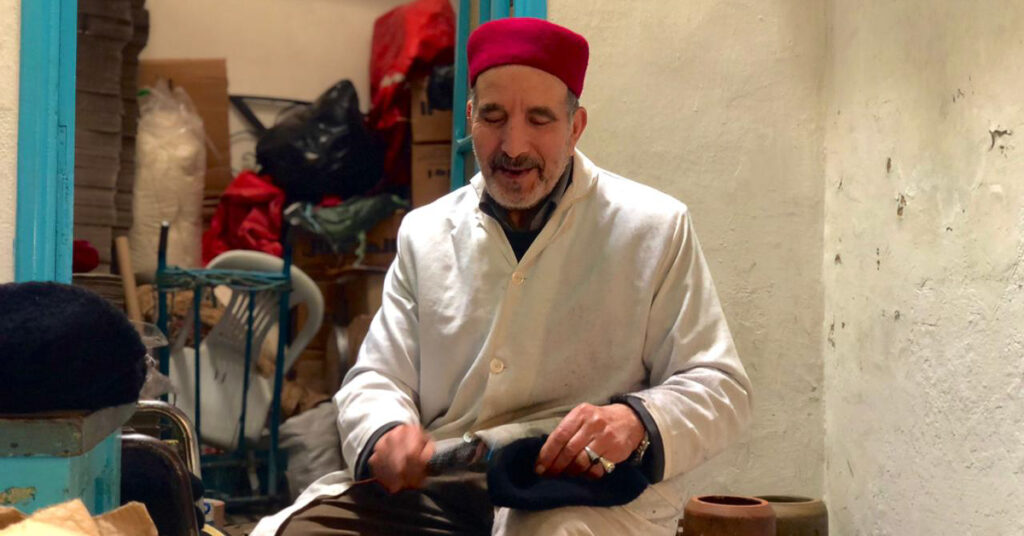
Now my chechia is well brushed and needs to go to Dawar Hisher, where artisans dye it, mould it and oven bake it for at least twelve hours. At this stage, my chechia is well shrunk from the beating up in Battan, well-brushed thanks to the Andalousi kardesh flower, and nicely overbaked after getting its red dye. So it comes back to my little shop, where I inspect it again, iron it, label it and pack it into a box that shows my name. It’s a brand of quality and trust since I am a fourth-generation chaouachi.
Now that my chechia has travelled across Tunisia in its production process, it’s time to travel the other half of the world; and I am ready to export to all my African clients!
The chechia is made and sold about five months after I had ordered the wool yarn. About 3000 families were part of the production process. About 50 tons are produced yearly of which only 5% is consumed locally. All managed from my 3m by 5m workshop at souk el Chaouachia, Tunis Medina. This is actually a reduction in production since the seventeenth century when chechia were Tunisia’s main export!
Today chechia is struggling to survive. 95% of chechia clients come from unstable countries. The production time is at least four months. The production process is 50% dependent on women working from home scattered in rural areas around the country, and most are over 50 years old. Your product must pass by the wool boiling factory in Battan, a building in desperate need of renovation, with 100-year-old machines.

Battan is the one and only wool felting factory in Tunisia. No kabbouss could become chechia, without passing through the beating up in a lot of water from the river Mejerda. The felting factory of Battan was constructed in 1901. It’s now a classified historical national monument and not one stone can be moved without experts’ intervention. And not one stone was ever moved since its construction, waiting for funding and restoration by experts. In fact, restoring Battan had been a national priority for tens of years. The beating machines that shrink the kabbouss into chechia have not been changed since 1901 and are in a constant state of maintenance. When the Majerda river floods, it flows inside th Battan felting factory and the whole production has to stop.
Now, here is the good news. Every true boiled wool chechia worn in Africa is made in Tunisia. The Tunisian chechia know-how has accumulated over eight centuries of production for Africa. The quality of the Tunisian chechia, made by thousands of Tunisian hands, produces a quality that no other nation was ever been able to imitate. Chechia is an underestimated national success story!
As one chaouachi said to me “Every day when I am ready to leave my house for work, I honour the chechia by placing it gently over my head. Because thanks to this little red boiled wool hat, I got married, educated my children, fed my family and many other families. We cannot let go of this generous little hat, we will do all we can to make it survive”.
About Leila Ben-Gacem
Leila Ben-Gacem is a social entrepreneur, Ashoka Fellow and founder of Blue Fish, a consultancy that designs and implements projects to improve the economic dynamics of cultural heritage and improve their resilience. Leila also founded Dar el Harka, a creative industry hub; Dar Ben Gacem, a boutique hotel and cultural catalyst in the medina of Tunis. Leila is also a founder and president of Mdinti, an economic interest group, for urban preservation and revival.
The photos were taken by Eya MkaddemWorkshop of Mohamed Ben Eissa Chaouachi Otil Ben Abdelkader ElJaoui
Comments
Do you sell to the UK?